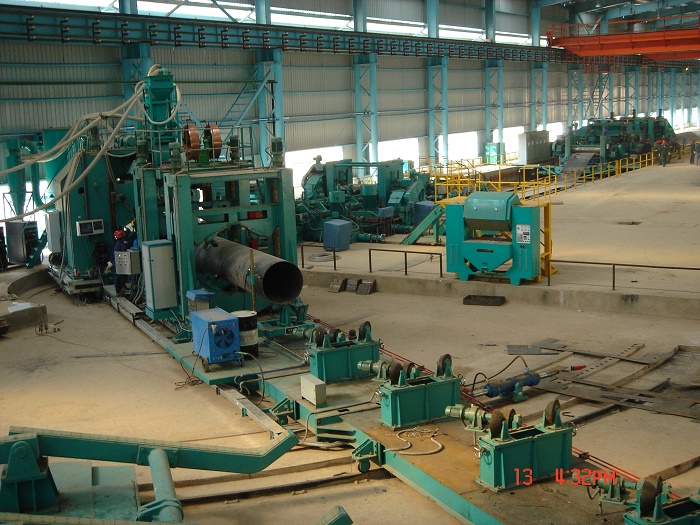
This pipe mill is a back-swing continuous SSAW Pipe Mill which has flying welding car and reliable progressive technology. The mill uses the leading-edge techniques of our company owns that including: Uncoiler bending strip tail at the end of coil, shearing&butt-welding unit using fission structure in butt-welding part in order to bevel the joint plate, quick edge milling machine and so on. These new techniques ensure the process and technology of mill, the quality and cost of production have reached the domestic and international advanced level.
This pipe mill is a whole set of mill which integrated machinery, electrical and hydraulic control system.
During the designing and manufacturing progress, the safeguard measure for equipments and operators were set for safety. For example: There are four sets of pressure sensor in the screw-down device which belongs to levelling machine; According to the sudden change of thickness, the self-protection unit is used in the depress device of pinching machine and main driver. Due to using the field-bus control system, operator can set the parameter of each machine with digitization setting screen. Through each power protection device and sensing element in the hardware unit, all kinds of operation parameters will be transmitted to the control centre for analytical processing, and then adjust the running status in time, all of these parameters will display in the HMI so that the operator can adjust the running status without delay, all of above measures effectively improve the operability and safety of the whole mill.
Forming process introduction:
Load the coil with crane onto the coil-car's carrier roller at first, and move the car into the center-line of Uncoiler, move the cone-head to clamp the coil tightly, centring the center-line of coil match with Main Driver line through operating buttons, then move the Peeler close to the coil and start the coil car roller motor to rotate in order to open the head of coil with Peeler working together, after the coil head goes into the straighten rollers the first bending could be done, then the coil head keeps going forward to Pinching and Levelling machine. After the coil head goes into the pinching rollers, depress down the pinching roller and feed the steel strip forward, the steel strip will go through the seven levelling rollers and keep going, the center-line of steel strip will keep centring with mill center-line by the Side Guide roller devices. After Shearing&Butt-welding machine, the steel strip will be sheared and butt-welded, then go into the Pinching roller machine and move forward into looper. All of the above unit machines is fixed on the Flying Welding Car which keep synchronous with Main Driver and realize the continuous producing for the pipe making work. After the looper the steel strip moves forward into Main Driver, the Main Driver supplys the total power force for forming force which overcome all kinds of resistance force e.g. Edge milling and forming resistance. Edge miller is consist of Facing miller and Bevelling miller, ensure the edge of steel strip continued and smooth, prepare for the on-line submerged arc welding and ensure the welding quality. After edge milling the steel strip will move into Prebending machine and Guide Board device which keep moving steady into the Forming machine, the forming process is finished by No.1, No.2, No.3 forming roller which bend the steel strip directly, and the sizing process is finished by No.4, No.5, No.6, No.7, No.8 forming roller. During the forming process the Lincoln welder will weld the connecting two edges inside and outside. After inside and outside welding parts the pipe will move into Pay-off table area, the pipe will be cut to length by Plasma cutter and Length Sensor device, then the pipe will be transported out of Pay-off table by Moving Car, repeat the cutting and moving off work over and over, ensure the continuous producing.